The Net Zero Procurement Playbook - Part 3/5: Transforming Manufacturing Emissions
- sobrunelle
- Mar 10
- 3 min read
Welcome to the third article in our five-part series on how procurement can drive organisations toward their net zero targets. After exploring renewable electricity sourcing and transportation, we'll now focus on another crucial lever: manufacturing emissions. As a procurement professional, your supplier choices and specifications can significantly influence how products are manufactured, making you a key player in reducing industrial emissions.
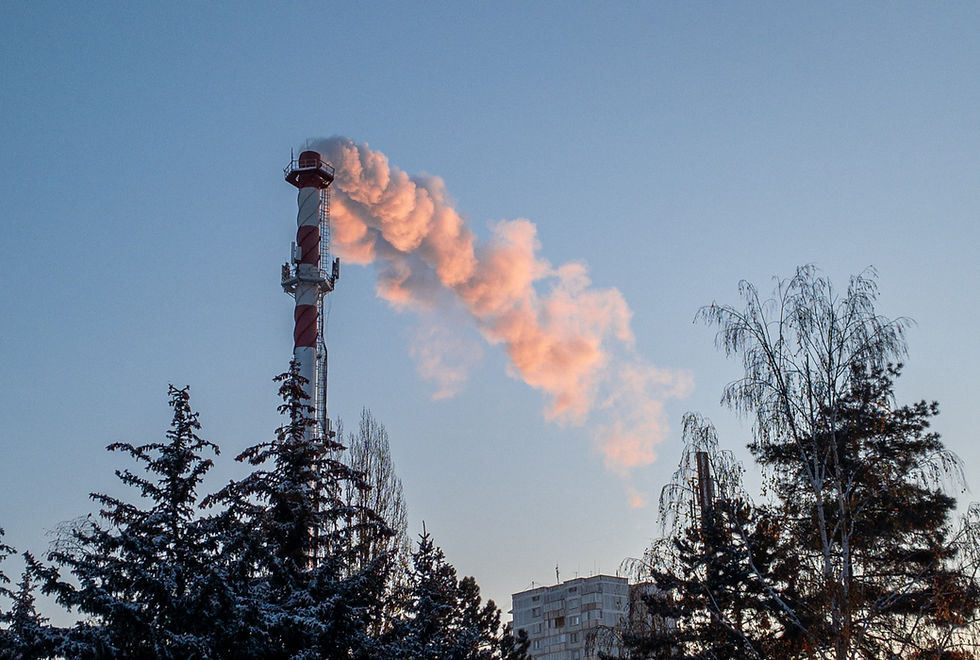
Using Less Heat: Efficiency First
Heat consumption represents one of the largest sources of emissions in manufacturing.
Here's how you can help your suppliers reduce their heat usage:
Insulation excellence
When selecting suppliers or specifying facility requirements, you can:
Require advanced thermal insulation technologies in manufacturing facilities
Include insulation specifications in your supplier audits
Look for partners who regularly upgrade their insulation systems
Consider insulation performance in your supplier scoring
Temperature control optimisation
Your procurement specifications can drive better temperature management:
Mandate precision temperature control systems
Request energy monitoring and reporting
Specify maximum temperature variance tolerances
Include temperature management in supplier performance metrics
Heat recovery systems
You can make waste heat recovery a priority:
Include waste heat recovery capabilities in supplier requirements
Favour facilities with heat exchange systems
Support suppliers in implementing heat recovery projects
Consider inter-plant heat sharing opportunities
Generating Low-Emission Heat: The Future of Industrial Heating
While reducing heat consumption is crucial, the remaining heat needs must be generated with lower emissions. Here's how you can influence this:
Electrification opportunities
Electric heat pumps can reduce emissions by 70-80%. You can:
Prioritise suppliers using electric heating systems
Support suppliers' transition to heat pump technology
Include electrification plans in supplier development programmes
Consider co-investment in electrification projects
Biomass solutions
Whilst renewable, biomass needs careful consideration:
Evaluate suppliers' biomass sourcing practices
Ensure biomass is genuinely sustainable
Consider local environmental impacts
Look for certified sustainable biomass sources
Green hydrogen potential
For high-temperature processes, green hydrogen offers promise:
Identify processes suitable for hydrogen conversion
Support pilot projects with key suppliers
Include hydrogen readiness in long-term supplier planning
Consider early adopter partnerships
Geothermal options
In tectonically active regions, geothermal energy provides consistent heat:
Map suppliers in geothermal-suitable regions
Support feasibility studies for geothermal adoption
Consider geothermal potential in new supplier selection
Include geothermal in supplier development plans
Using Less Resources: Beyond Energy Efficiency
Resource efficiency goes hand in hand with emissions reduction. Here's how you can drive improvement:
Waste reduction
Your procurement requirements can minimise waste:
Mandate zero-waste manufacturing approaches
Require advanced reprocessing technologies
Set specific waste reduction targets
Include waste metrics in supplier scorecards
Packaging optimisation
Influence packaging choices through:
Minimising packaging volume and weight requirements
Specifying multiple lifecycle use designs
Setting recycled content requirements
Implementing packaging return systems
Water conservation
Water usage often correlates with energy consumption:
Require closed-loop water recycling systems
Specify precision water usage monitoring
Set water reduction targets
Include water efficiency in supplier assessments
Material efficiency
Your specifications can drive material efficiency:
Require use of lightweight, high-performance materials
Specify precision manufacturing techniques
Set material waste reduction targets
Support material innovation initiatives
Your Action Plan: Making It Happen
To implement these strategies effectively:
1. Assess current state
Map your suppliers' manufacturing emissions
Identify highest-impact processes
Benchmark against industry best practices
Prioritise improvement areas
2. Set clear requirements
Develop clear technical specifications
Create measurable performance targets
Establish monitoring protocols
Define improvement timelines
3. Support supplier development
Create supplier development programmes
Offer technical assistance
Consider co-investment opportunities
Share best practices across your supply base
4. Monitor and report
Track emissions reductions
Measure cost impacts
Document success stories
Adjust strategies based on results
As a procurement professional, you have significant influence over manufacturing emissions through your supplier selection and development activities. While the challenges may seem daunting, remember that each improvement in manufacturing efficiency contributes to both emissions reduction and cost savings.
Stay tuned for our fourth article, where we'll explore how procurement can drive emissions reductions in agriculture.
Need help developing your procurement emissions reduction strategy? Our team of experts is ready to help you create and implement a tailored approach for your organisation. Contact us at info@beeaware-consulting.com or through our contact form to start transforming your manufacturing procurement practices.
Comments